Design for Economy—Framework for Design Excellence
Good design adds economic value for owners, occupants, the community, and the planet—regardless of the project size and budget.
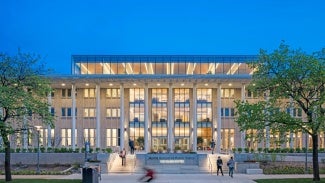
- How do we provide abundance while living within our means?
- How do we design robust projects that enhance economic, natural, intellectual, and experiential resources?
- How will the design choices balance cost with long-term value?
- How can the performance of this project be improved in ways that are cost and design neutral?
Focus topics
- Building size
- Material use and reuse
- Operational requirements
- Financing and incentives
- Community links
- Cost estimating and value engineering
Design for Economy toolkit
If you can do only one (or a few) thing(s):
- ZERO CARBON: Reuse an existing building if possible and reuse materials wherever appropriate.
- ZERO CARBON: Right-size the program early and keep the square footage as efficient as possible while supporting occupant experience and managing design for change.
- RESILIENT: Identify the proposed service life for the building and create a plan to adapt to hazard risk over time.
- EQUITABLE: Design to support a vibrant local economy, maintaining diverse populations and supporting local resources and trades.
- HEALTHY: Healthier buildings equal healthier people. Balance operational and maintenance requirements to improve occupant health and well-being, improve community health outcomes, and lower household health care expenses.
Sustainable development is an approach to economic planning that attempts to foster economic growth while preserving the quality of the environment for future generations. Designing for the economy is interwoven into every aspect of a project, including project financing, site selection, building programming, space planning, evaluation of building systems, selection of materials, and cost estimating/value engineering. The economic benefits of sustainability are well-established: operating cost savings, shorter payback periods, and increased asset value. Design for economy benefits not only owners but also building users, local communities, and the planet. The principle focuses not just on immediate finances but also on preserving and enhancing social and environmental capital.
Good economic design is sustainable design. There is a misconception in the industry that sustainable design adds cost so only a few projects with high budgets and ambitious goals can afford to be “sustainable,” but this isn’t accurate. While some features will result in additional costs upfront, many strategies that result in better buildings are cost-neutral or provide initial savings and operational economy. These savings may be critically important when dealing with project types such as affordable housing, where the cost impacts of energy and water use are borne by people least equipped to afford excessive consumption.
Reusing an existing structure is another strategy that can lower initial costs and preserve community history. Adaptive reuse finds value in the existing fabric of our cities, improving the shell and interior and repairing gaps in the urban environment. It also reduces the embodied carbon of the project through reuse of carbon-intensive structural materials such as aluminum, steel, and concrete. Building reuse has other benefits for economy and equity: The cost breakdown for a reuse project is typically 60% labor/40% materials, compared to a typical new build at 55% labor/45% materials. Reuse ensures that more resources remain in the community.
Design for economy means assessing design decisions from a holistic and synergistic standpoint rather than by line item, uncovering indirect opportunities to reduce and enhance a building’s life cycle costs and improving the community's social and environmental economy. For example, when selecting a roof system, consider systems that have synergistic benefits such as stormwater retention (blue roofs), heat island reduction, or biophilia (green roofs). The whole is greater than the sum of its parts in architecture and value engineering.
Building size
A bigger building will cost more, use more resources, and consume more energy than a smaller one. Right-sizing decreases a building’s square footage to save construction costs and material resources and reduces the project’s operational and embodied carbon impact. A deep analysis of the building program can yield efficiencies in building size and opportunities to use a single space in multiple ways.
Site selection offers many opportunities for cost savings. Consider connectivity, walkability, and mixed-use potential. Also consider resilient design and life cycle thinking by evaluating the site location and its relationship to observed and foreseeable hazards. Placing a well-designed building in the wrong location can waste economic resources and place lives and investments in danger.
Actions:
- Space should be seen as a resource to conserve, just like water or energy. Efficient use of space that also maintains design, scope, and building quality is a good indicator of economic design.
- Strategies for reducing square footage include efficient building planning, designing program elements to overlap, and eliminating program redundancies. Program for typical building operations and not for the occasional overflow events.
- Consider incorporating spaces that can serve multiple uses for the owner or other entities, depending on time of day. For example, new schools in New York City have a “gymnatorium” rather than a separate gym and auditorium.
- Building efficiency ratio (net square footage divided by gross square footage) measures the percentage of conditioned space dedicated to building program versus the overall gross square footage of the building. While typical building efficiency ratios differ among building types, a higher efficiency ratio means a more efficient use of space and resources.
- Program buildings to participate in collaborative consumption models, which prioritize shared use over ownership. For example, providing a shared goods library or a cleaning and maintenance service in a multifamily building can reduce the need for everyone to own a drill, vacuum cleaner, ladder, etc. That, in turn, can allow for a reduction of building square footage.
- Find opportunities to develop collaborative and reciprocal relationships within the community to share spaces and develop resilience. Sharing resources is a core concept of the circular economy.
- Consider if there are underutilized local spaces that could be used for some program activities. Also consider if some spaces can be used by others, offering future revenue generation for the client. Examples include school auditoriums leased out to community groups and daytime coworking spaces in restaurants that are open only in the evening. Consider the resources dedicated to parking and advocate for smaller minimum parking standards. Prioritize parking for shared cars and bicycles.
- Recognize that the topic of economy extends beyond the walls of your building, impacting the urban development scale as well. There is a compounding negative effect created by larger buildings and new greenfield construction, which consumes valuable land resources in cities. This can increase owner and building-user costs in several indirect ways. For example, increased land use leads to larger urban footprints, requiring more time, energy, infrastructure development, and monetary resources for citizens to move around that city. Thousands of hours of economic productivity are lost each year in cities due to long commutes. The cost of building and maintaining the additional urban infrastructure needed to serve that larger urban footprint is often borne by building owners and citizens of a community.
Material use
Consider reusing an existing building or renovating it before deciding to build new construction. Recycle and reuse materials on-site where possible. Reuse has the largest impact on reducing embodied carbon and preserves resources for the future. Reuse, and especially preservation, keeps more labor in the local economy and supports highly skilled labor.
Actions:
- Reuse an existing building if possible. New construction typically uses more resources and has a larger embodied carbon impact than rehabilitation. Even if only part of the building can be reused—for example, the foundations and structural frame—the benefits for economy and sustainability are great.
- Choose locally sourced and produced materials to fit the established context, capitalize on local knowledge and trades, and reduce the embodied carbon emissions associated with transportation. Using materials that are locally sourced also supports the local economy.
- Reusing salvaged materials may also be a good economic decision for the immediate construction project as well as the local economy. Supporting a local reuse material exchange network and refurbishing trades will build local reuse ecosystems.
- Limiting material use is a good indicator of economy. This can be accomplished by eliminating superfluous materials to decrease total cost per square foot and embodied carbon impact of a project. Consider using materials that serve multiple functions. For example, structural shear walls are intrinsically impact-resistant and can serve as sound and fire barriers. Reducing redundancy in the finish materials, such as floor coverings over concrete or gypsum board over plywood, can reduce waste and recovery time after a disaster event.
- A life cycle assessment (LCA) can inform material selections and efficient material use by evaluating various environmental impact categories. This process can help architects decide on the appropriate service life, replacement cycle, and level of investment for different types of materials. See additional information about LCAs under Design for Resources.
- Identify the proposed service life for the building and create a plan to adapt to hazard risk over time. An LCA is especially important when future hazards or disasters are included in the analysis.
- Plan for the future: The strategies that add first costs often provide long-term savings. For example, adding renewable energy systems will cost more initially, but they can become cost-neutral or cost-positive over time, not just through operational savings but also through indirect benefits such as avoiding interruptions.
- Work with manufacturers and general contractors to understand the best ways to successfully make assemblies and materials that can be reused. Modular items, such as interior partitions and millwork that are attached with mechanical fasteners, are easy to relocate when needs change, preserving not only their embodied carbon but also their value.
- When designing tenant spaces, consider the lifespan of the project and design accordingly. How can a design incorporate elements that will last for multiple tenant interior cycles? How can finishes be made flexible to shift with tenant needs?
Operational requirements
The greatest test of economy is how the building performs over the entire life cycle. Designing for optimal building performance in energy, water, and waste decreases the operational costs of a building. Decreasing operational costs does not always require a higher upfront investment; if it does, this cost can often be reclaimed as a “net-positive” transaction within a reasonable payback period. AIA is taking action to eliminate all building carbon emissions by 2040.
Actions:
- Reduce maintenance requirements by choosing more durable materials or materials that require less intensive cleaning or have longer replacement cycles. How will materials weather to provide a low-maintenance finish? How will materials perform if a disaster strikes? Confirm that durable and long-lasting materials do not use chemicals of concern or create intensive emissions to produce.
- How do the building systems promote individual wellness, comfort, advancement, and productivity? Comfortable spaces improve health and well-being while reducing absenteeism and other negative health impacts.
- How do the building systems promote resource savings? Heating and cooling accounts for about 43% of all energy use in the country. Buildings account for 12% of total water consumed in the U.S. Operational efficiencies save money as well as resources.
- Eliminate fossil fuels in the building for heating, water heating, and other tasks. Otherwise, it may be costly to upgrade systems in order to adhere to future codes and policies that limit carbon emissions.
- How does the building design promote waste diversion from landfills every day? Is recycling convenient and prioritized?
- Consider the potential range of uses for the structure 50 and 100 or more years in the future. How flexible are the spaces to accommodate future uses without significant reconstruction?
- Hazard mitigation protects lives, improves safety, prevents property loss, and decreases disruption of daily life. According to the NIBS Natural Hazard Mitigation Saves 2019 report, adopting hazard mitigation measures can save $6 for every $1 of investment in response and recovery costs depending on the level of protection and the hazard addressed.
Financing & incentives
Many programs support design excellence and climate action, but sources of funding are constantly changing. Research local, state, and national incentives, grants, and financing options to justify long-term investments to improve performance. Examples include energy-cost payback, water savings, measured productivity gains, property-assessed clean energy (PACE), third-party power purchase agreements (PPA), and more.
Actions:
- Seek equitable economic solutions that improve opportunities to access capital and resources for disadvantaged communities. Consider if a design approach or building project could result in a synergistic relationship with the community, providing economic opportunities over the life of the project.
- Consider emerging funding models that leverage improved outcomes for worker productivity, student learning, and reduced sick time to fund healthy building retrofits that improve indoor air quality.
- Consider with clients if efficient or healthy building features would yield higher rents, differentiate their product in the marketplace, reduce risk of vacancy, or present an opportunity for community engagement or community resilience building.
- Search for historic or other tax credits for rehabilitating existing buildings.
- Find out if the municipality offers fee reductions for development that follows green building standards.
- Research utility companies’ ratepayer-funded energy conservation and efficiency programs.
- Develop literacy on terms capital investors and developers use: Net present value (NPV), return on investment (ROI), cash flow positive, and simple payback period (SPP). Advocate for improvements directly to the investors who finance projects.
- Learn about buildings as material banks (BAMB), a concept from the circular economy where building materials can be disassembled and reused in the future, sustaining their value. Innovative financing methods that reward this approach are being developed. Corporations with a strong commitment to environmental, social, and governance (ESG) rankings may already identify green building as a core objective. Work within the UN Principles for Responsible Investment.
- Perform a benefit-cost analysis to determine the potential payback for hazard resilience measures. Find out if conducting a third-party climate-risk assessment to mitigate the risks of climate change at the project scale would benefit the client’s proforma, financing, or insurance rates. See Design for Change for more information.
Community links
The local economy is the economy that matters most to a stationary building. It is essential that local residents participate in determining the future of their community and benefit from the construction and occupation of the project.
Actions:
- Locally sourced materials and construction systems form a link to the local economy. Choose materials with which local craftspeople have experience and give them some freedom to express their skill.
- Include workforce training opportunities during the construction of a project. These opportunities teach valuable skills and provide the experience necessary for career growth and future employment.
- Provide opportunities for local artists to install art, which creates local economic benefits and helps create links between a building and a community.
- Encourage clients and building owners to include or consider programs that benefit the local community. For example, designing a space that serves the needs of the owner but can also be rented out to a community organization can produce additional revenue for a building owner during underutilized hours and benefit the community at the same time.
- Find opportunities to salvage materials wherever possible. Many building materials outlive the buildings they once served, and these embodied resources may have many years of service life ahead.
- Provide opportunities for small and disadvantaged businesses to participate in the construction phase by offering pre-bid meetings, inviting local tradespeople, and writing specifications to support equitable project delivery models.
Cost estimating & value engineering
Economy is the balance between cost and value. All design teams understand the cost ceiling, but designers of excellent projects focus on elevating a project to deliver maximum value.
Actions:
- Opportunities for cost savings decrease over the design process, so ensuring a robust and thorough conceptual design is key.
- Climate adaptation measures are easiest to justify when one element does the work of many, or an investment pays back daily. Sun-shading devices might also shield intense rainfall. Passive House standards reduce heat gain or loss and reduce the size of mechanical equipment. Solar panels and a battery backup can power a building during a hurricane and reduce operating costs for lighting, receptacles, and appliances. These are “low regret” options that yield benefits even in the absence of a hazard event and “win-win” measures that manage several climate risks at once.
- Utilize an integrative design process to connect design choices to community and project team values to increase the likelihood of multi-attribute design choices surviving the value engineering (VE) chopping block.
- The key term in the VE process is value, an increase in the worth of a building design when weighed against cost. The worth can be considered in many ways, not just the first cost.
- The VE process can be better understood as “value enhancement.” The primary question to ask in all VE is, how can we get the most for the least amount of investment? This could be initial cost, longer service life of components, better performance, increased sustainability, multi-functions of a space, or anything that increases the value of the building for the owner.
- The VE process can contribute to the value of a building by providing a multipronged approach, considering the whole life and service of the building. It can be directed to every aspect of a building, from site selection through the planning and programming process, to the systems and products used to construct the building.
- Read the ROI: The economic case for resilient design to learn key talking points to convey to clients, civic leaders, vendors, and other architects the importance of integrating resilient and climate-adaptive design to protect social welfare, increase value, and contribute to the built environment’s sustainability and resilience.
- AIA Guide to Building Life Cycle Assessment in Practice can help answer numerous questions that arise during the design and construction of a green building. An LCA can reinforce the decisions taken by architects by providing scientific justification.
- Avoiding cost premiums on green projects is not only possible, but also a good idea. "BuildingGreen: “How to Build Green At No Added Cost” focuses on simple, effective designs that can deliver savings for years to come.
- "Ellen MacArthur Foundation Report “What Is the Circular Economy?" provides a framework for an economy that is restorative and regenerative by design. Its “Circular Economy in the Built Environment“ publication with Arup provides more details. “Building a Circular Future” by the Danish architects GXN is a comprehensive resource on designing for disassembly, material passports, and the circular economy.
- The Database of State Incentives for Renewables & Efficiency includes a comprehensive list of programs to support funding high-performance aspects of your project. “How to Calculate and Present Deep Retrofit Value” is an easy-to-follow guide to facilitate translation of high-performance buildings into economic value for investors and clients. Healthy Buildings: How Indoor Spaces Drive Performances and Productivity by Joseph G. Allen and John D. Macomber. Makes the case for healthy buildings and offers strategies for building them.
- Buildings as Material Banks is a European initiative to forward a circular economy of building materials, the site has extensive resources.
Design Excellence case studies: Explore four projects demonstrating successful economic design
Explore four COTE® Top Ten award recipients demonstrating successful economic design.
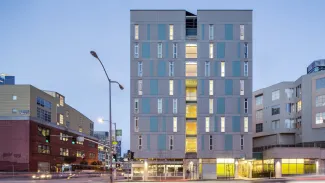
Rene Cazenave Apartments
San Francisco, California | Leddy Maytum Stacy Architects
The Rene Cazenave Apartments demonstrate the city’s commitment to creating a community based on social, financial, and environmental sustainability and integration.
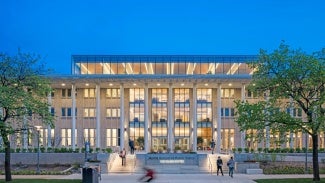
Keller Center–Harris School of Public Policy
Chicago, Illinois | Farr Associates, Woodhouse Tinucci Architects
The Keller Center doubled student enrollment within the building with only a modest rooftop addition through modeling, improving space utilization, and flexible space usage.
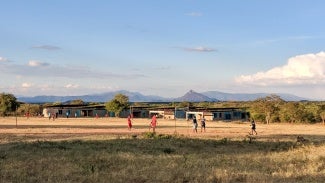
Asilong Christian High School
West Pokot, Kenya | BNIM
At the Asilong Christian High School, BNIM continually balanced first costs against long-term benefits, leading to decisions such as purchasing a brick machine so local laborers could make high-quality bricks—reducing transport costs, and developing a local skilled workforce.
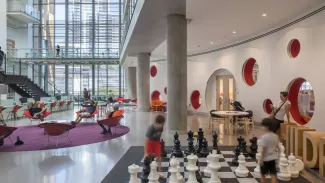
Austin Central Library
Austin, Texas | Lake|Flato, Shepley Bulfinch
Architects for the Austin Central Library looked at adding revenue-generating spaces in the programming phase.
This publication is designed to provide accurate and authoritative information in regard to the subject matter covered. It is published and distributed with the understanding that the publisher is not engaged in rendering professional services. If professional advice or other expert assistance is required, the services of a competent professional person should be sought.
AIA does not sponsor or endorse any enterprise, whether public or private, operated for profit. Further, no AIA officer, director, committee member, or employee, or any of its component organizations in his or her official capacity, is permitted to approve, sponsor, endorse, or do anything that may be deemed or construed to be an approval, sponsorship, or endorsement of any material of construction or any method or manner of handling, using, distributing, or dealing in any material or product.
If you have any questions or feedback regarding the Framework for Design Excellence, please let us know.
Learn how the framework inspires and provides a toolkit for sustainable, resilient, and inclusive design.
Explore the next chapter of the Framework for Design Excellence—Design for Energy.